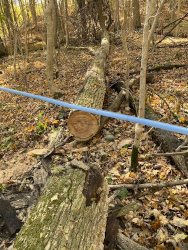
2021 Season Prep
We’re getting ready for the 2021 sugaring season and there’s always something fun to do.
We’re nearly complete now (mid-January)…
…so let’s take a look at what we’ve been up to.
In the field . . . 500+ Taps for 2021!
Field preparations began in early November with the clearing of fallen trees and branches from the sap lines that lead to collection tanks. We had a couple of big ones down this year. Then came the cleaning and installation of the two primary collection tanks with total holding capacity of 560 gallons as well as the installation of 6 additional 55-gallon sap collection tanks.
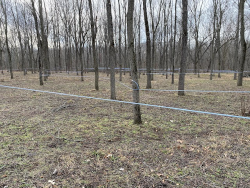
New sap lines and spiles (taps) are being installed as needed to replace older lines. In addition, a new 3/16-line system is also being put in place in our walnut grove. This year we are experimenting with diaphragm-pump-assisted gravity system for walnut sap collection.
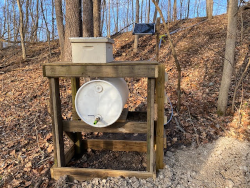
Here we have 85 trees on two lines flowing into a tank with the help of a 12-volt, 1GPM diaphragm pump. A solar powered trickle charger will help keep the battery fresh – and the sap flowing. (We hope. It’s a test, as we really don’t know if it will work. But that’s part of the adventure.)
We haven’t had time to count them all, but our estimate is about 120 walnut taps and 400+ sugar maple taps. So there’ll be even more to do later.
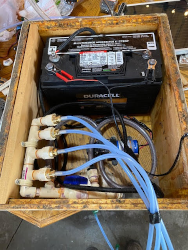
New Equipment
To process all that sap into delicious Springboro Tree Farms maple, walnut (hopefully!) and bourbon-barrel aged maple syrup we invested in a new reverse osmosis machine with four times the capacity of our first machine. Our new Deer Run Maple 250 RO removes about 50% of the water from sap at a flow rate of 250 gallons per hour. We typically take sap from 1.5% sugar incoming sap to 12% or 14% sugar and then process through our Sunrise Metal Spitfire Evaporator. The RO reduces energy costs and cooking time by 60% or more. And the product we produce today is much better than what we produced just a few years ago.
But there’s always a catch. The new higher capacity RO machine required increased incoming sap flow and that called for the replacement of all ¾-inch incoming plumbing with 1-inch lines. And because RO capacity increased, holding tank capacity for permeate water more than doubled from 210 gallons to 500 gallons. So there’s been a lot to do.
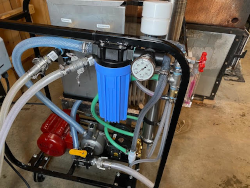
This year we also purchased a new Water-Jacketed Canning vessel manufactured by Sunrise Metal. Designed to bring syrup to a food-safe bottling temperature without creating “hot spots” that may cause more ninter (sugar sand) to form in the syrup or darken the syrup. We’re also motorizing our filter press which will really help the whole filtering process…especially if we are fortunate enough to collect a good amount of walnut sap. As we’ve noted before, the process to make walnut syrup is the same as with maple syrup but the filtering is more of a challenge for sure.
Cleaning
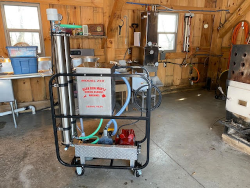
And then there’s the deep cleaning of everything in the sugar shack. We’ve installed all new sap lines inside the sugar shack. We always use non-toxic FDA lines and stainless steel tanks…and cleaning products (such as Star San®) designed for commercial use.
Supplies
Supplies such as evaporator pan cleaner, filter press paper and diatomaceous earth (DE), glass bottles, caps; labels, RO pre-filters, etc. etc. all need to be checked and ordered to ensure we are ready for the season.
Maintenance
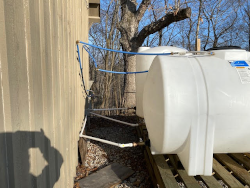
This year we’ll rebuild our filter press with a new diaphragm and valves. So that’s next up on the To Do List.
In addition sap transfer pumps, lines and couplings in the field and inside the sugar shack all need to be tested for functionality and leaks.
And finally we look at tapping supplies such as drills and bits, replacement sap line, and make up new replacement drop lines with spiles that will be needed when we start tapping trees.
Equipment set-up
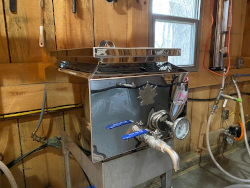
Set up of the evaporator and related systems is always a fun day. This includes cleaning the arch (wood-burning stove below the pan), checking seals and valves on the evaporator connections as well as cleaning and assembling the evaporator itself.
Another important part of equipment set up is the preparation of the reverse osmosis machine. This includes a soap wash and rinse as well as the installation of the plumbing required.
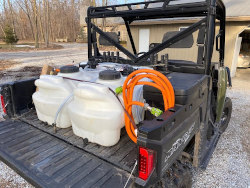
And then there is the inspection, cleaning and installation of collection tanks, pumps and hoses on the ATV and tractor.
Almost time to go to work
With all this done, it’s time for a break before we really go to work!
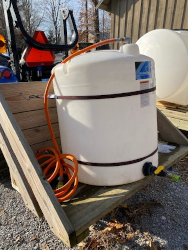
Well…until some of us go to work.
Has anybody seen Jim?